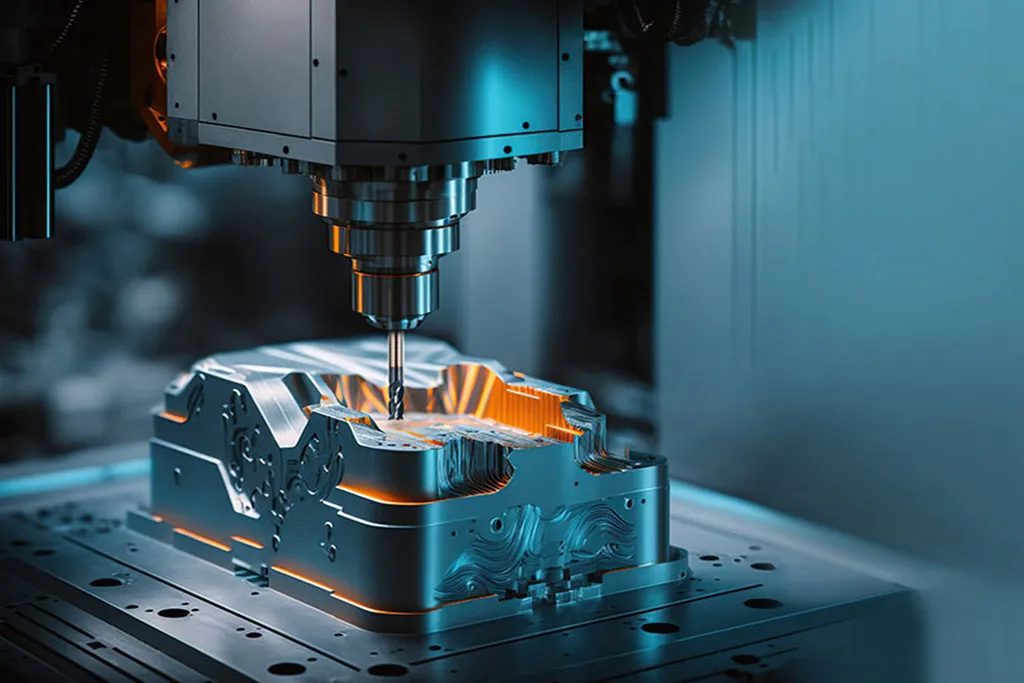
1. Fused Deposition Modeling (FDM)
Fused Deposition Modeling (FDM) is one of the most popular and accessible 3D printing methods. FDM printers use thermoplastic filaments, such as PLA, ABS, and PETG. The printer heats the filament to a molten state and extrudes it through a nozzle, building layers to form the object.
Advantages:
- Affordable: FDM is widely available and budget-friendly.
- Versatile: It supports various filament types and colors.
Applications: FDM is ideal for hobbyists, rapid prototyping, and creating functional parts. It’s used in fields like education, consumer goods, and automotive prototyping.
2. Stereolithography (SLA)
Stereolithography (SLA) is a resin-based printing method. SLA printers use a UV laser to harden layers of liquid resin, forming detailed models with smooth finishes. The printer moves layer by layer, curing each one to create the final product.
Advantages:
- High Precision: SLA offers extremely fine details and smooth surfaces.
- Wide Range of Resins: Options include standard, flexible, and high-temperature resins.
Applications: SLA is ideal for creating detailed models, such as jewelry, dental molds, and medical devices. It’s commonly used in industries requiring intricate parts with fine resolution.
3. Digital Light Processing (DLP)
Digital Light Processing (DLP) is similar to SLA but uses a digital light projector instead of a laser. This projector flashes entire layers of light at once, curing the resin faster than SLA. DLP printers can produce detailed models with accuracy and speed.
Advantages:
- Speed: DLP is often faster than SLA due to its whole-layer projection.
- Detail: It produces highly detailed parts with excellent resolution.
Applications: DLP is popular in dentistry, jewelry, and product design. Its high speed and accuracy make it ideal for industries that need quick and precise prototypes.
4. Selective Laser Sintering (SLS)
Selective Laser Sintering (SLS) uses a high-powered laser to fuse plastic powder layer by layer. Unlike FDM or SLA, SLS doesn’t require support structures, as the surrounding powder stabilizes the object. This makes it possible to print more complex shapes.
Advantages:
- No Supports Needed: The powder acts as a support, allowing for complex designs.
- Durability: SLS-printed parts are strong and can withstand stress.
Applications: SLS is popular in engineering, automotive, and aerospace industries. It’s suitable for functional prototypes and small-batch production, especially when parts need durability and complexity.
5. MultiJet Fusion (MJF)
MultiJet Fusion (MJF) is an advanced method developed by HP. MJF printers use a fusing agent, detailing agent, and heating element to selectively fuse plastic powder layers. This technique creates smooth, functional parts with excellent detail and durability.
Advantages:
- Strength: MJF parts are strong and isotropic, meaning they’re equally durable in all directions.
- Speed and Precision: MJF prints faster than many other methods with high accuracy.
Applications: MJF is common in functional prototyping, end-use parts, and manufacturing of components that require both strength and detail. It’s used in sectors like electronics, automotive, and consumer products.
6. PolyJet Printing
PolyJet printing uses photopolymer droplets, which are jetted onto a build platform in thin layers. UV light then cures these droplets, creating complex parts with multiple colors and materials in a single print. PolyJet is one of the few methods that allow for multi-material and multi-color printing.
Advantages:
- Multi-Material Capability: It can print with different materials in one job.
- High Resolution: PolyJet produces models with a smooth finish and fine details.
Applications: PolyJet printing is ideal for prototypes that require multiple materials or color, such as medical models and consumer product prototypes. Designers often use PolyJet for visual and functional testing.
7. Direct Ink Writing (DIW)
Direct Ink Writing (DIW) involves extruding a paste-like material to build layers. DIW printers are versatile, as they can handle materials that aren’t strictly thermoplastic. Although less common, DIW can print flexible or specialized polymers.
Advantages:
- Material Versatility: DIW can print materials not possible with other methods.
- Adaptability: The extrusion-based process allows for customized material blends.
Applications: DIW is used in industries needing flexible or specialized materials, such as biomedical devices and research prototypes.
Choosing the Right 3D Printing Method for Plastic
The best method depends on several factors:
- Budget: FDM and SLA are generally more affordable, while MJF and SLS are more costly.
- Required Detail: SLA, DLP, and PolyJet offer high detail, suitable for intricate designs.
- Material Needs: Each method has different material compatibility, from flexible resins in SLA to durable powder in SLS.
Conclusion
3D printing plastic offers numerous options, each suited to different needs. Methods like FDM, SLA, DLP, and SLS provide unique benefits, from speed to intricate detail. With advancements in technology, 3D printing continues to offer creative solutions for prototyping and production. Selecting the right method depends on project requirements, budget, and design complexity. These methods keep expanding possibilities, making 3D printing an essential tool across industries.